Setting up an MPG Jog Pendant in LinuxCNC
CNC jog pendants are super useful devices for quick setup and configuration of CNC machines. A quick search for CNC jog pendant on AliExpress turns up a bunch of results. For this post, I'll cover connecting a wired jog pendant with ESTOP to a Mesa 5i25 FPGA card to control a 3 axis CNC mill.
The config below works for me. The plethora of hardware configs out there mean this article likely won't work for you verbatim, but it's my hope that it provides a good starting point for other configs.
Please note that I got this config working on LinuxCNC 2.9.0-pre0. It should also work on 2.8.*, but will not work on anything before the joints/axes split.
Hardware
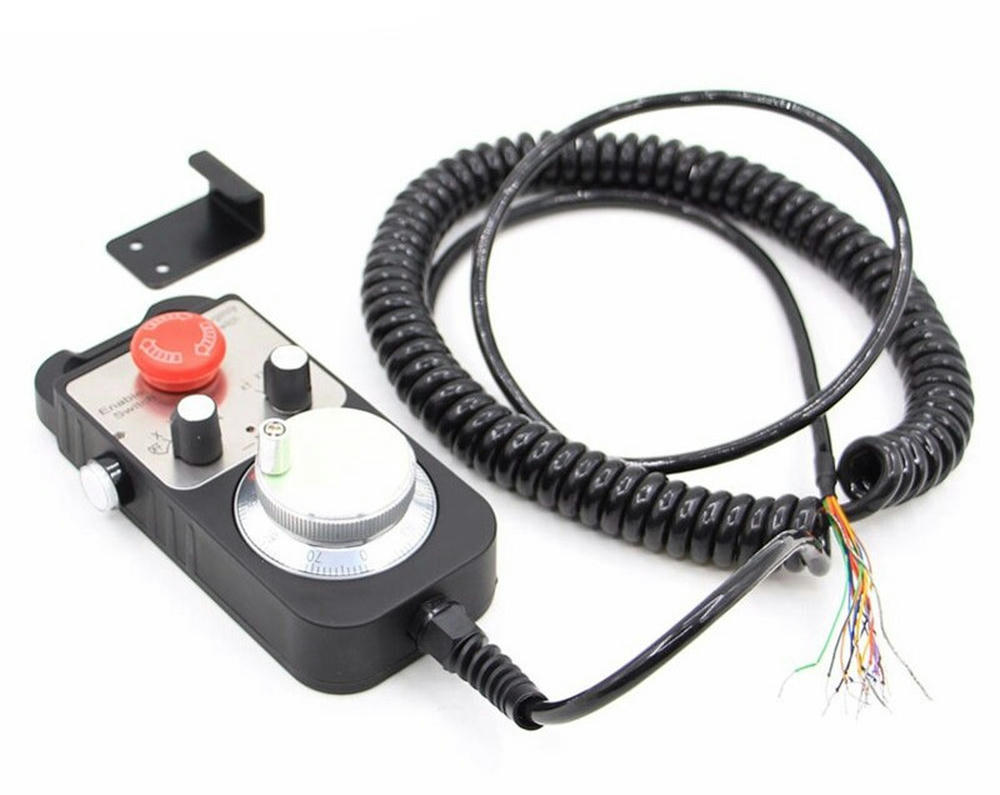
This is the jog pendant I'll be using.
It provides estop, axis select, multiplier and encoder outputs on a bunch of bare wires as seen in
the image. I'm going to connect it to the internal P2
connector of a Mesa 5i25 FPGA card, so I'll
trim the bare wires and solder them to a DB25 cable-end connector in a bit.
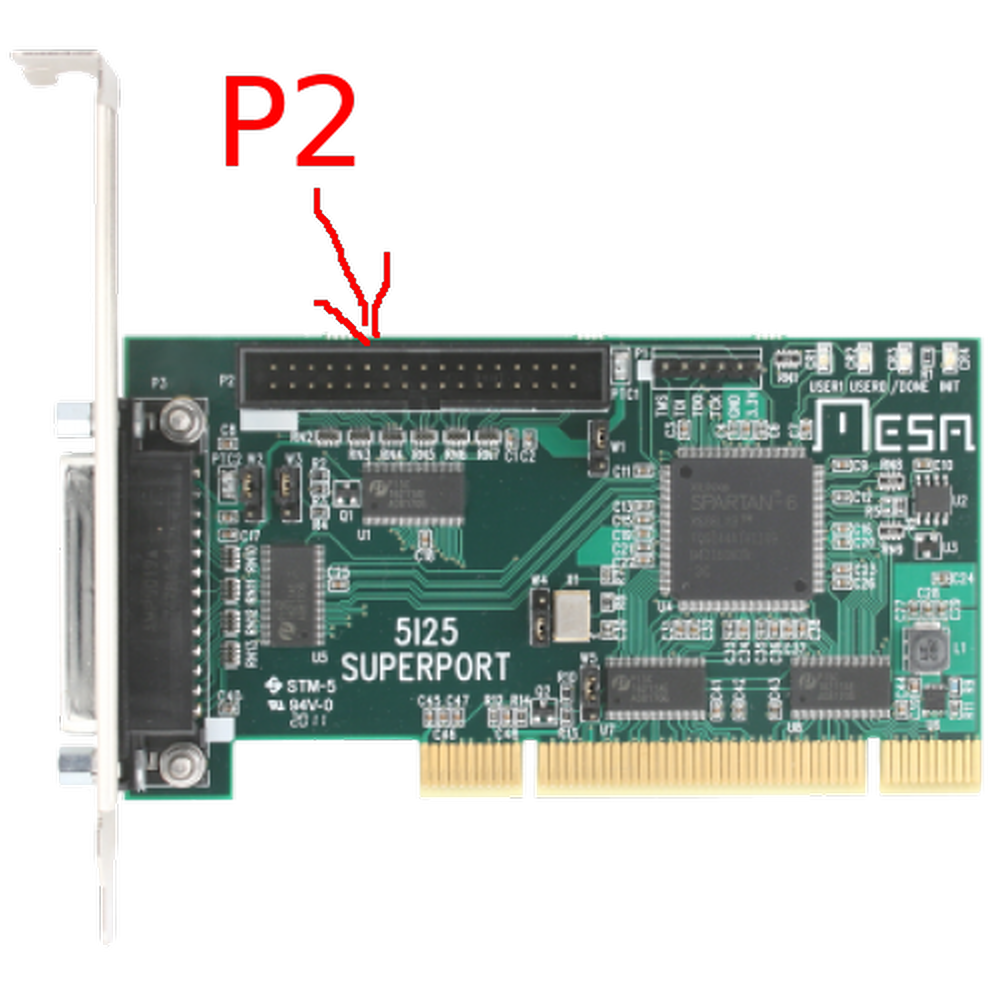
I'm using a Mesa 5i25 FPGA card through a DB25 breakout cable (like
this one) connected to P2
. Other Mesa cards with
parallel port breakout options like the 6i25 should also work, but are untested.
The Mesa card can optionally provide +5V to external circuitry on the last 4 pins of the parallel
port connector. This must be enabled for the jog pendant to work. From the manual, ensure that
jumper W1
is in the UP
position.
For reference, here's an image of the breakout cable:
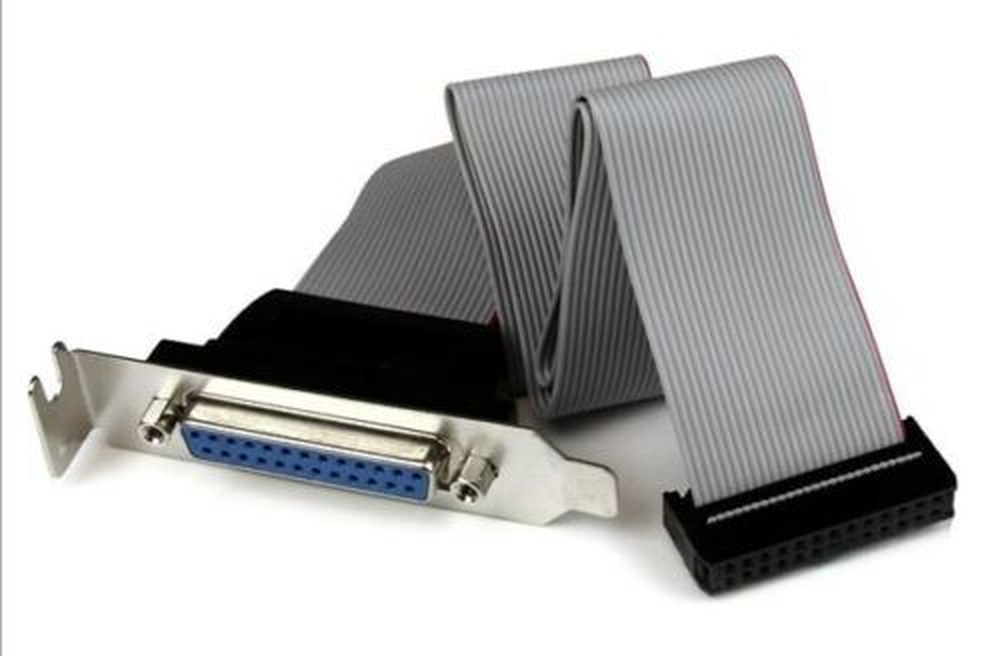
Soldering up the jog wheel connector
We now need to solder a DB25 connnector to the jog pendant cable so it can be plugged into the Mesa card. The exact pinout doesn't matter too much as connections can be remapped in software, but in my setup the jog wheel encoder is bound to pins 11 and 12.
This is the full pinout:
Name | DB25 connector pin | Hostmot2 GPIO (we'll use this later) | Wire colour |
---|---|---|---|
ESTOP | 4 | gpio.023 | Blue/black |
ESTOP gnd | 21 | - | Blue |
Encoder +5V | 25 | - | Red |
Encoder gnd | 20 | - | Black |
Encoder A | 11 | encoder.01.input-a | Green |
Encoder B | 12 | encoder.01.input-b | White |
Encoder A- | - | - | Purple |
Encoder B- | - | - | Purple/black |
Common | 19 | - | Orange/black |
Select axis X | 1 | gpio.017 | Yellow |
Select axis Y | 14 | gpio.018 | Yellow/black |
Select axis Z | 2 | gpio.019 | Brown |
Select axis 4 | 5 | - | Brown/black |
X1 | 15 | gpio.020 | Grey |
X10 | 3 | gpio.021 | Grey/black |
X100 | 16 | gpio.022 | Orange |
LED+ | - | - | Green/black |
LED- | - | - | White/black |
Encoder +5V
, Encoder gnd
and Common
are connected to ground and +5V, with the 5V supplied by
the last 4 pins by enabling the auxiliary power on the Mesa card by setting jumper W1
to the UP
position.
I'm leaving the inverted signals of the encoder disconnected for simplicity. If you need the noise suppression features of differential wiring, you'll need to add some external circuitry to deal with that - the Mesa encoder inputs are single-sided.
I'm also leaving the enable LED disconnected because I can't be bothered to hook it up.
Mesa card configuration
I'm using the 5i25_prob_rfx2
bitfile for the Mesa 5i25. It seems to be a pretty general purpose
config for these cards. Other configs might work, but the pinout could be different so YMMV.
The pendant is mostly simple GPIO, but you'll need to add an extra encoder to your Mesa config when
loaded. In your <machine name>.hal
file, find the loadrt
line and change it:
- loadrt hm2_pci config="firmware=hm2/5i25/5i25_prob_rfx2 num_encoders=1 num_pwmgens=0 num_stepgens=3"
+ loadrt hm2_pci config="firmware=hm2/5i25/5i25_prob_rfx2 num_encoders=2 num_pwmgens=0 num_stepgens=3"
This will add an extra encoder called encoder.01
for the HAL config to use later.
The above hm2
config is for a 3 axis mill with a spingle encoder. Because I'm already using one
encoder for the spindle, I'm upping the encoder count to 2
. This puts the second encoder signals
on pins 11 and 12 of the DB25 connector on P2
which we'll use for the jog pendant. If you've got a
different number of encoders, you might have to change the connector pinout in the table above or
use a completely different Mesa card/tutorial. Sorry.
Jog pendant HAL configuration
Create a new HAL file called mpg.hal
and add the following:
# MPG (jog wheel) config
#
# MPG is plugged into secondary (internal) connector via a DB25 breakout cable. Pinout can be found
# at https://wapl.es/cnc/2020/02/23/linuxcnc-jog-wheel-setup.html
#
# This config requires `numencoders=2` when loading the Mesa component. It uses the second encoder,
# as the first is connected to the spindle motor
# Add component to mux axis selection into the selected axis
# --- JOINT-SELECT-A ---
# --- JOINT-SELECT-B ---
# --- JOINT-SELECT-C ---
# --- JOG-INCR-A ---
# --- JOG-INCR-B ---
# --- JOG-INCR-C ---
# --- ESTOP-EXT ---
# ---jogwheel signals to mesa encoder - shared MPG---
# ---mpg signals---
# for axis x MPG
# for axis y MPG
# for axis z MPG
# connect selectable mpg jog increments
# Note that increments of 0.025 scale to 0.1 due to 4x scaling of encoder pulses vs clicks
Some observations:
- I'm using the
in_not
inverted pin values. The 5i25 has weak pullups, so pins are active low and default to high (TRUE
). - I'm using
mux16
instead ofmux4
because I'm lazy. - Because the jog wheel is a quadrature encoder, there are 4 counts per "click". The jog scales of
0.00025
,0.0025
, etc are the1x
,10x
and100x
markings on the pendant panel divided by 4. - The
selected-jog-incr
,joint-select-*
andjoint-selected-count
signals are wired to both thejoint
andaxis
signals. This is required to make the axes move after homing, and is a result of the joints/axes split that happened around LinuxCNC 2.8/2.9.
Finally, to load this extra HAL config into the machine, add a line to the [HAL]
section in
<config name>.ini
:
[HAL]
HALUI = halui
HALFILE = <config name>.hal
+ HALFILE = mpg.hal
POSTGUI_HALFILE = postgui_call_list.hal
SHUTDOWN = shutdown.hal
Now you should be good. If something's not working check the HAL Meter for GPIO states and
encoder.01
values.